In the meantime Enrique Perez published a plug-in script called Skeinforge.bsh for ArtOfIllusion that also converts 3D objects to G code extruder paths. It is written in the Beanshell script language, which is Java like. I decided to try both approaches, as in theory a G code parser would allow me to use either.
Enrique posted some new scripts that process G code and drive the RepRap hardware using a Python SNAP protocol driver written by greenarrow, so I didn't even need to think about writing a G code parser, I just cut and pasted a few lines from Enrique's.
Before letting it drive my machine I thought it would be a good idea to look at the paths on screen. I knocked up a little script which used my HydraRaptor simulator to draw them. The script is just a few lines of Python that use TkInter.
It was soon apparent that Enrique's code had a bug that left off some of the outline, but apart from that it looked very promising because it has the ability to do sparse infill. That speeds up building objects, saves plastic and reduces warping so it is very worth while. Not only that, it had a novel infill pattern. Instead of parallel lines like this: -
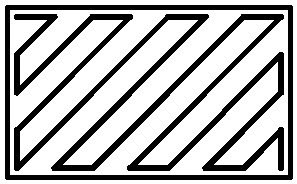
He moves the ends together so that the outer wall is stronger: -
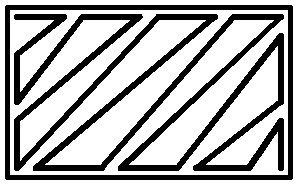
This looks like a good idea because it makes the outer wall effectively two layers thick but probably gives a bit less warping than a second continuous layer would give.
In order to communicate the results to the forums I came up with the idea of making an animated GIF showing all the layers in sequence. This turned out to very easy using Google and Python. The Python Image Library (PIL) can make GIF files and I found a script called gifmaker.py which takes a list of images and uses PIL to calculate the deltas and write out an animated GIF.
Enrique fixed the bug very quickly, here is the sliced extruder pump body: -
The red lines are moves without filament flowing (ideally) and the each new section of filament is a different colour.
And here is the same object sliced by the reprap host :-
A side effect of Enrique's algorithm is that the corners get rounded, however I don't think that matters too much because the filament has a minimum bend radius anyway. The main downside is that beanshell script is very slow, so it takes longer to slice than it does to extrude at the moment. A faster PC will probably sort that.
The first object I tried to make was this opto mounting bracket from the RepRap Darwin: -
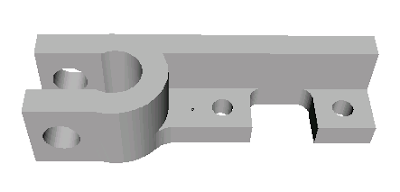
I choose it because it is small, so does not take too long, but reasonably complex with a horizontal hole. Here is the sliced path from Enrique's script: -
And here is my first attempt at making it: -
This is PCL extruded onto MDF, 0.625mm filament extruded at 10mm/s with the fan on, no interlayer pauses.
A bit hairy due to the extruder not being able to stop the filament flow quickly, but I was quite pleased with it for a first attempt. It is too tall due to a bug in my code and its not the latest version, which has teardrop shaped holes to make the overhangs less than 45°.
Here it is cleaned up a bit: -
It is 50% filled which is probably not appropriate for this size object in PLA but that part is fully functional I think.
Enrique was pleased to see it as he doesn't have a machine to test his code with. A perfect partnership, he writes all the hard bits in beanshell script and I write the easy stuff in Python!